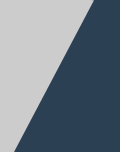
Related Datasheets
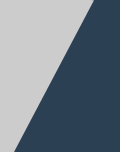
Related Brochures
Request a Quote
Please fill in the boxes on the contact form and a member of the team will contact you directly for a quotation.
As the lightest of the refractory metals (a group of metallic elements that exhibit extremely high melt points and heat resistance), niobium is a highly sought-after material with applications in aerospace, electronics, nuclear power and defense. In this article, we explore the properties that set niobium apart from the other refractory metals, as well as its current applications and potential for use in future technologies.
In its elemental form, niobium is a light gray transition metal that belongs to a group of elements known as refractory metals. Like other refractory metals, niobium exhibits a very high melting point (2477 C); however, it stands apart from the other refractory metals due to its relatively low density. At only 8.57g/cm3, niobium has a density similar to that of nickel and copper, making it the lightest of the refractory metals.
Niobium bears many similarities to tantalum, another refractory metal. The two metals occur naturally together in the form of the mineral columbite, and were long thought to be the same metal. Niobium and tantalum share many physical and chemical properties: their high ductility at room temperature makes these two metals the most versatile of the refractory metals1 and both are protected by a pentoxide (i.e., Nb2O5 and Ta2O5).
Niobium is a key component in high-temperature nickel based superalloys. Thanks to their high-temperature strength and relatively low density, these alloys are extremely valuable for aerospace applications.
In addition to its high strength, ductility, heat resistance, and comparatively low density; niobium also exhibits superconductivity at cryogenic temperatures, and is used to manufacture superconducting magnets for medical and research applications.
Aerospace components are typically required to withstand high temperatures, thermal fatique, and high mechanical loads. These performance requirements, coupled with the need to reduce weight wherever possible in aircraft and spacecraft design, mean the aerospace industry has some of the highest material requirements of any industry.2
Refractory metals such as molybdenum, tungsten and tantalum are commonly used in for aerospace applications due to their ability to provide strength in the 830°C – 1830°C region.3 However, thanks to its lower density, niobium is indispensable to the industry; offering high-performance physical properties in the form of a relatively lightweight and easily-worked metal.
Refractory metal alloys are continually being developed for high-temperature aerospace applications.4 One such alloy which has achieved widespread use is C-103: a complex refractory alloy consisting primarily of niobium, with additions of 10wt% hafnium, 1wt% titanium, and trace amounts of other elements.
Key to the success of C-103 is its low density and exceptional strength across a very wide temperature range – from cryogenic temperatures up to 1482 C.4 Having been used almost since the beginning of the space age, C-103 is a proven material and among the leading refractory metals used in propulsion and space exploration technologies.
Importantly, C-103 is easy to form – something that is certainly not true of all refractory metals, nor of many refractory ceramics or composites developed for aerospace. In spite of its high melting point, C-103 can be hot, warm, or cold worked using traditional techniques to produce flat and round products. C-103 can also be readily machined and TIG welded without significant loss of ductility enabling complex aerospace components to be easily fabricated.
C-103 is used in a variety of aircraft components, from thrust augmenter flaps in gas turbines to high-temperature valves. Research is currently underway to develop niobium-based alloys for next-generation aerospace technologies such as heat pipes to dissipate heat from hypersonic leading edges and nose cones.
As well as being a refractory metal, niobium belongs to another exclusive group of elements: the elemental superconductors. These materials – which include indium, tin and lead – are united by the fact that their electrical resistivity drops abruptly to zero when they are cooled below a certain critical temperature ( ).
Niobium’s critical temperature for superconductivity is 9.3K – the highest critical temperature of any elemental superconductor.5 Niobium has therefore been the natural choice for the development of higher temperature superconducting alloys, which include niobium-tin (Nb3Sn, ) and niobium-germanium (Nb3Ge, K). Niobium alloys are used to manufacture superconducting magnets for use in medical MRI machines and NMR machines for analytical chemistry applications. The LHC particle collider even uses niobium-titanium magnets to corral high-energy particles around its beamline. Plans are currently underway to upgrade these magnets to a higher-performance niobium-tin alloy for the next phase of the LHC’s operation.6,7
As well as excellent mechanical strength and heat resistance, niobium alloys can also exhibit superior resistance to radiation. This earns niobium numerous applications in the nuclear industry, alongside other refractory metals like tungsten and molybdenum.
Boasting extremely low neutron absorption cross-sections and good resistance to liquid metals, niobium zirconium alloys are commonly used for structural elements in nuclear reactors.8 Niobium also finds use in high-temperature irradiation-resistant instrumentation in high-temperature reactors.9
Niobium alloys are also attracting interest for the construction of next-generation nuclear fission reactors. Recent research shows that these materials may be suitable for building structural elements in Generation IV fission reactors thanks to their superlative retention of mechanical strength at very high temperatures.10
Elmet Technologies (formerly H.C. Starck Solutions) is one of the biggest global providers of niobium for industrial applications, providing niobium and niobium-based alloys in the following forms:
In addition, Elmet Technologies (formerly H.C. Starck Solutions) leverages its expertise in manufacturing and process development to create custom niobium solutions for its customers. To find out more about our capabilities in niobium, niobium alloys and other refractory metals, get in touch with a member of the Elmet Technologies (formerly H.C. Starck Solutions) team.
References and Further Reading
Please fill in the boxes on the contact form and a member of the team will contact you directly for a quotation.